城市地下交通线路工程大直径盾构隧道
盾构机,它的正式名称叫做全断面隧道掘进机,平时大家可能很少见到它,因为它一般都在地下或是山洞里工作,是建造地铁、铁路、公路、隧道等的利器。因为系统复杂、集成度高,也有人把它称为机械制造皇冠上的明珠。
盾构刀具作为盾构机的“牙齿”,是盾构掘进系统的关键部件,直接影响到盾构机的掘进速度、施工成本和工程质量。作为吉林省科技进步一等奖获得者的凌远科技股份有限公司,多年来通过持续技术攻关,将成果应用于国内外数十个高难度地质条件的高强度硬岩隧道或复杂地层隧道项目中,促进我国盾构机零部件核心技术不断突破。
在掘进中逆袭
世界上第一台盾构机是法国工程师布鲁诺尔发明的。直到1953年,中国才引入第一台盾构机,中国盾构机的使用发展历史只有不足70年,但是如今全世界都争相抢购中国盾构机,从国外进口到全球领先,中国盾构机逆袭成功。
盾构机如今已经被中国做到了“白菜价”,让西方痛失了又一个可以赚钱的神器,以前盾构机被西方定义为高端科技产物,想要引进一台盾构机,往往需要花费几千万美元。为了防止中国掌握核心技术,拒绝出售生产线,拒绝培训维护人员,赚足了售后的利润,而且一旦出了故障,维修盾构机就会变得非常麻烦。
上世纪90年代末,中国城镇化开始起步,基础设施建设加速。中国是地大物博的国家,国内有很多城市需要建设地铁,挖掘隧道,用基建助力经济发展。1997年,为了建设西康铁路秦岭隧道,中国第一次进口了两台德国盾构机,两台二手盾构机花了7亿元,相比传统的隧道钻爆法,盾构机施工不仅效率大幅提升,而且施工过程安全性大大提高。但是,在享受安全高效的同时,我国也不得不接受高昂的设备费用,和并不顺畅的售后服务。
直到2008年,通过我国科研人员的不懈努力,研发出中国第一台盾构机“中铁一号”。在此基础上,我国盾构机开始井喷式发展,国内盾构机行业开始快速崛起,从此开始替代了进口,转而使用国产设备。
从0到1,从完全不能生产到如今国产化率达到90%,中国在盾构机领域的发展速度,比在高铁和民航客机领域的发展速度还要快。之所以国产产品能完全取代国外产品,主要还是因为掌握了盾构机核心技术,一台盾构机包含上万个零部件,比如刀具和主轴承,刀具刀盘的设计研发,一直是盾构机国产化的重要课题。
跟普通机械设备不同的是,盾构机是定制化产品,每一台设备都需要结合实际的工程单独设计,不同的地质、不同应用场景,会有不同的需求。“比如砂卵石地层,对刀具磨损是非常厉害的,所以我们就给装备配备上合适该地质的刀具。” 凌远科技股份有限公司董事长张凌说。
在应用中攻关
盾构机最关键的技术是它前部作为磨损件的刀具。这些刀具要满足高硬度、高韧性、高强度等特点,其生产技术曾长时间被德国“卡脖子”,想更换只能购买德国的配套产品。2002年攻关团队负责人张凌便开始组建技术团队进行攻关,致力于研发、生产国内隧道掘进机(TBM)配件。
在研制的初期,刀圈选材为行业普遍采用的H13钢材作为原材料,采用传统的自由锻造工艺,同时采用传统的方式对刀圈进行热处理,致使锻造后的刀圈毛坯尺寸不规则,加工余量大,制造成本极高。技术团队通过对产品不断提升和创新,自首批成果应用于磨沟岭隧道工程掘进试验后,几年间,团队结合工程统计数据、平行产品对比,不断提升产品技术指标。通过经验积累与分析,将刀圈毛坯的锻造方式进行改进,由传统的自由锻造改为辊锻方式,并且优化了热处理工艺,其使用性能已达到进口刀具的90%以上。虽然在刀圈质量上有很大的提升,但刀圈毛坯重量仍然较大,成本没有明显降低。
此后,技术攻关团队对刀圈的材料进行了突破性的改进,并研发出了新型FSD、WG系列高耐磨、高硬性、高韧性材料,通过接近真实服役工况的数字化模拟分析技术,对刀圈的性能进行模拟分析;利用电渣二次重熔技术,改进原材料的组织,通过万吨级高压近净成形技术,将刀圈毛坯一次锻压成形;最后通过真空热处理技术,结合以特殊的过程热处理工艺,真正提高了刀圈的核心性能,既“硬”又“韧”,各项性能指标均优于进口刀圈,同时大幅度降低了刀圈的制造成本。
“技术攻关不能单打独斗,要各自发挥优势,懂研发的不懂工程,懂工程的不懂研发,要解决研发与应用的壁垒,就要联合。”张凌说。为此,攻关团队重新组建,形成了产学研用的专攻技术团队,相继与东北电力大学、吉林大学、中南大学、石家庄铁道大学等多所高校开展产学研合作,结合多年施工案例、大量一手工况数据,对现有刀具存在的不稳定因素进行排查,对进口刀具进行全面分析实验,研制出性能更稳定、破岩效果更优异的刀具产品。
2014年,由研发团队组建的凌远科技股份有限公司正式成立。为加快技术研发,公司陆续购入成套的高精尖现代化生产和实验设备,通过技术团队试验和刀具装配工程师对掘进现场刀具失效的监测记录,对刀具关键部件刀圈的改进作出深入研究,研发出一套创造性的核心技术,并以此为依托,承担起了吉林省重大科技成果转化项目。
水利工程引水隧道小直径TBM刀盘出洞
在减量中提质
盾构机有着“钢铁蛟龙”之称。盾构机挖掘进度直接影响整个工程的进度、施工成本和工程质量。作为盾构机的“牙齿”,每天多挖掘一米,都是在节约成本,缩短挖掘时间,如果刀具“质”不提高,就会产生非正常磨损,导致刀具消耗过大,每次停机换刀具就要至少耽误两个小时,所以刀具的质量、稳定性尤为重要。
2016年,团队参与引汉济渭工程秦岭隧道项目,涌水、塌方、岩爆、高温地热及高强度硬岩等诸多困难因素叠加,构成隧道施工的世界级难题。施工中由于岩石强度高、石英含量非常高、节理发育程度低,同时岩爆冲击危害强,当岩石硬度超过130MPa时,刀具消耗量极大,挖掘工作不得已缓慢进行或准备购买进口刀具。团队在经过地质勘探报告分析后,拿出研发的拳头产品在秦岭隧道现场做实装互换对比试验,与美国某知名滚刀比较磨耗率等关键性能绩效参数,超过进口滚刀33.67%,及时地解决了施工难题。“实验结束后,王梦恕院士很欣慰,他说刀具虽然是整个隧道建设中小之又小的一个部件,但这证明了我们科研团队为隧道工程配套而努力的结果,他的最大愿望就是让我国拥有世界一流的隧道产业工程配套能力,服务祖国和人民。”张凌说。
除此之外,团队承担着多个国家战略级TBM / 盾构隧道工程的刀具任务,如云南大瑞铁路工程、川藏线铁路林芝段色季拉山隧道工程、滇中引水工程、南水北调工程、珠三角水资源配置优化工程、海外“一带一路”项目如尼泊尔喜马拉雅山巴瑞巴贝引水隧道工程、以色列特拉维夫红线项目、格鲁吉亚高加索山脉KK公路隧道工程、斯里兰卡上依拉黑运河引水隧道工程等等。与大多数装备公司不同,“我们专门喜欢啃硬骨头,别人干不了的我们来,别人干不动的我们上,我们不求项目数量,但力求我们参与的每个项目都以‘质’取胜。”张凌说。
从初创团队到公司走向市场,20多年来,持续攻关成了团队的一种工作习惯,以科技创新驱动生产力,追求核心技术全自主,而试验检测能力是保证技术主动权牢固自主掌控的关键。在这一坚定的基本理念的驱动下,团队先后创建“吉林省盾构与掘进刀具技术科技创新平台”“吉林省盾构与掘进刀具技术重点实验室”和企业技术中心,以隧道掘进民族工业发展为己任,秉承工匠精神,追求卓越,做强“中国之刃”。
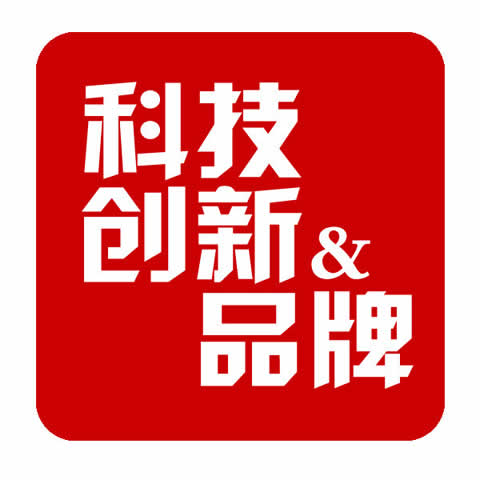