摘要:Z型口分段翻身吊装采用龙门吊和翻身工装的配合,解决由于分段错口造成的吊装时倾斜及定位困难问题。已知的翻身工装存在着安装困难、材料浪费,通用性差等问题。我们通过应用TRIZ理论,采用功能分析、因果链分析、资源分析等工具剖析了问题产生的根本原因,并应用功能裁剪、技术矛盾等工具,最终得到了13个解决方案。对所得的方案进行了技术评价,并根据实际需要选择了解决方案3作为实施方案,最终应用解决方案对翻身工装进行了创新改进,解决了原有工装人工安装困难等问题。
引言
常规船大开孔分段进行分段划分时,由于考虑板尺及分段重量等因素,大开孔的横向边缘通常布置在分段的中间及附近区域,分段合拢口在艏艉方向不是直线,而是呈类型Z字形。由于此类型分段横向刚度大于纵向刚度,在进行龙门吊3钩吊装布置时,需要按刚度强的方向的来设计翻身吊耳,既横向翻身,因此主钩吊耳需要布置在靠船中合拢口处。但因合拢口不是直线,Z字形错口的形状会导致主钩的吊耳之间无法布置在一条直线上,主钩吊耳安装位置不一致会使得分段翻身过程调平困难,影响总组定位,导致后续工作无法顺利进行。
1 现有技术方案
1.1 现有技术改进前情况
目前常规的解决方案是利用翻身工装,配合B型吊耳使用。翻身工装与吊耳之间通过卸扣连接,使用时通过工装将分段抬起。工装长度弥补了错口尺寸,销轴连接可让工装绕着吊耳进行90°旋转,保证整个吊装过程中主钩两吊点受力状态同步,可以解决由于错口造成的分段吊装时倾斜及定位困难问题。(如图1)
1.2 现有技术存在的问题
由于工装长度长,强度原因需要使用厚板,使得工装整体重量过大,分段是反向建造,重量太大无法直接安装,需要工人配合手拉葫芦使用,费时费力,另外工装孔距固定,通用性差,无法满足不同错口尺寸。
1.3 常规解决途径及问题
目前有焊接型接长工装和辅助工装小车两种方法解决工装过重难以安装问题,但存在造价高,操作不便,浪费材料等问题。因此我们需要对翻身工装进行创新改进,提高安装效率,更好的服务于生产。
2 TRIZ理论概述
TRIZ理论是一种专门解决发明创造问题的方法体系,通过跨行业、多学科之间基础知识的交叉融合总结归纳出发明问题背后的普遍规律,进而指导广大工程技术人员更加快速有效的寻求发明问题解决方案。通过先将工程实际问题转化为TRIZ问题模型,再使用TRIZ各种创新工具进行解题,得到多种TRIZ方案,多种TRIZ方案还需要结合各行业专业知识,得到最终的TRIZ解决方案。针对现有翻身工装存在的不足,本文通过TRIZ理论中的部分典型工具来进行问题解决。
3 问题分析与求解过程
3.1 问题描述
Z型口分段翻身吊装采用利用龙门吊和翻身工装的配合,解决由于分段错口造成的吊装时倾斜及定位困难问题。目前现有的翻身工装都存在重量过大,人工反向安装困难,通用性差等问题,施工人员需要使用滑轮或者工装小车来解决此问题,费时费力,且存在安全隐患。本文利用TRIZ理论寻求突破处理这一短板限制的有效方案。
3.2 IFR理想解
依据TRIZ理论,在解决问题开始之前,要先抛开各种限制因素,仅通过理想化来定义问题的最终理想解,通过明确理想解所在的方向和位置,以保证在解决问题过程中始终沿着此目标前行并获得最终理想解。
我们的最终理想解是实现工装自动安装,对此我们提出方案1和方案2。
方案1:设计一种工装自身携带的能够方便吊车或叉车对工装实现起升的装置。
方案2:设计一种工装自身携带的能够方便人工对工装实现轻松起升的装置。
3.3 功能分析
系统的功能模型图是由系统组件和组件中相互作用的关系组成,可以很容易得出存在问题的功能和组件的相互作用关系。系统功能模型图如图2所示,可以看出,翻身工装对人工安装来说是阻力,阻力是有害的限制,需要去掉或减少这种力。提出技术方案3和方案4
方案3:优化翻身工装结构形式,减小重量或便于安装。
方案4:使用辅助工具帮助人工进行安装,节省人力。
3.4 因果链分析
利用因果链分析可以帮助我们通过层层因果分析找到隐藏于问题背后的根本原因,从而全面彻底解决问题。对于安装困难问题,我们通过现场实际情况结合因果链工具分析出以下因果分析图(见图3):
通过因果链分析得出结论,工装的结构形式重量大,无高效辅助安装工具,导致人工安装困难。并提出技术方案5和方案6
方案5:优化翻身工装结构形式,减小重量或便于安装。
方案6:使用辅助工具帮助人工进行安装,节省人力。
3.5 资源分析
根据系统功能分析结果,从物资、能量、功能这三个方面进行资源分析,分析结果如下表1所示:
根据资源分析结果,得到技术方案7:使用(升力)起升工具资源将翻身工装提升安装,省去人力安装。
3.6 功能裁剪
功能裁剪是TRIZ中一种改进系统的方法,通过裁剪,将由功能分析得到的问题功能所对应的的组件进行删除,而将其所执行的有用功能利用系统或者超系统的其他组件替代执行,实行功能再分配,从而改善整个功能模型。通过裁剪掉中间辅助工装手拉葫芦,使用其它具有相同功能的X1组件进行替代(见图4)。提出技术方案8和9:
方案8:去掉对人产生阻力的手拉葫芦,采用其它可以省力的装置。
方案9:去掉对人产生阻力的手拉葫芦,在工装上增加一个可以使其实现升降功能,而无需要人工操作的装置。
3.7 技术矛盾(见图5)
技术矛盾是技术系统中两个参数之间的矛盾,即当用某种办法去改善技术系统的一个参数(或一部分)时,该系统的其它参数 (或其它部分)就要恶化。
要解决的技术矛盾发生在(重量)与(方便安装)之间,发生在(工装安装)的时候。
问题模型--对应的39个通用工程参数
改善的参数为操作流程的方便性,恶化的参数为静止物体的重量
组成通用工程参数为:6、13、1、25
对应查看阿奇舒勒矛盾矩阵表得到如下创新原理,并提出技术方案10、11、12和13:
方案10: 多用性原理,使用其它具有安装功能的工具辅助安装。
使用液压小车或自动升降工装进行辅助安装,节省人力。
方案11:反向作用原理,使工件从上向下安装。
使用吊车将工件进行吊起从上向下进行安装。
方案12:分割原理,工件拆解成多件方便安装。
将翻身工装设计成组合件,使用时进行组合安装。
方案13:自服务原理,设计工装件自动安装功能。
将工装设计成一种自动行走或升降的装置,实现自动安装。
4 技术方案整理与评价
4.1 全部技术方案及评价
我们利用TRIZ方法得出了以上13个解决方案,并对13个方案进行相似技术方案整合,得到以下解决方案。
通过整合方案3、5,提出解决方案1:优化翻身工装结构形式,减小重量。
通过整合方案4、6、7、10,提出解决方案2:设计具有移动及升降功能的安装小车,辅助安装翻身工装。
通过整合方案1、2、8、9、10、11、12和13,提出解决方案3:改进工装件结构,使其具有可移动及升降功能。
我们对解决方案进行分析对比(见表2)
4.2 最终方案确定
通过对整合后的解决方案对比及最终评估,选择解决方案3作为实施方案,最终创新设计了新型翻身工装结构(见图6)。其结构特点及功能优化如下:
1、新型翻身工装采用的是上部T型梁,下部双T型梁的组合式结构,组合体件之间开设多个定位孔,使组合件之间可以进行长度调节,使主吊孔能探出分段合拢口,弥补了各种类型分段的错口尺寸,保证整个吊装过程中主钩两吊点受力状态同步,解决了由于分段错口造成的吊装时倾斜及定位困难问题。
2、新型翻身工装安装及使用过程简单快捷,摒弃了传统工装吊耳安装时由于重量大,需要利用手拉葫芦或者辅助安装小车工具等繁琐过程,采用此工装安全可靠,且极大缩短了吊装作业时间。
3、工装下部结构设计了升降机构,使工装具备了升降功能,工装上部和升降机构下部加设万向轮,方便其移动和升降运动。
5 实施效果及应用推广
采用新型翻身工装+B型吊耳使用可替代传统的E型吊耳+结构接长,极大降低施工周期和施工成本。
若采用翻身工装,按目前我司西区吊车工位使用情况,只需要设计6套基本可以满足需求,每套工装的制作成本为4000元,工装总成本预计需要24000元。考虑吊耳的重复利用率,E型55T吊耳单次使用成本为390元,B型55T吊耳的单次使用成本为250元。
采用新方法,用B型55T吊耳配合工装代替E型55T吊耳,既每只吊耳能节省140元,采用此方法,连续安装170只B型吊耳,就可以收回工装制作的成本。
以我司8万5项目20条船为例,全船分段及子分段共需300个左右E型55T吊耳,通过此方法可节省140*300*20-24000(工装成本)=81.6万元。采用此工装配合B型吊耳,可以持续产生经济效益,达到节约成本、提高工作效率的目的。
6 结束语
习近平总书记曾强调,创新始终是推动一个国家、一个民族向前发展的重要力量。而TRIZ 的理论体系打破了固有的设计创新模式,应用TRIZ工具进行有效地问题解决,帮助工程设计人员者改变思维模式,寻找问题根源,并获得突破技术问题瓶颈的思路,从而得可靠有效的解决方案。
本文以TRIZ创新理论为指导工具,对翻身工装进行了创新改进,最终达到了节约成本、提高生产效率的目的。
参考文献
[1]黄浩.船体工艺手册[J].国防工业出版社,2013年
责编/马铭阳
注:本文为国家科技部“基于超大型智能原油船创新方法集成应用示范”项目(编号2018IMO040200)资助的成果之一。
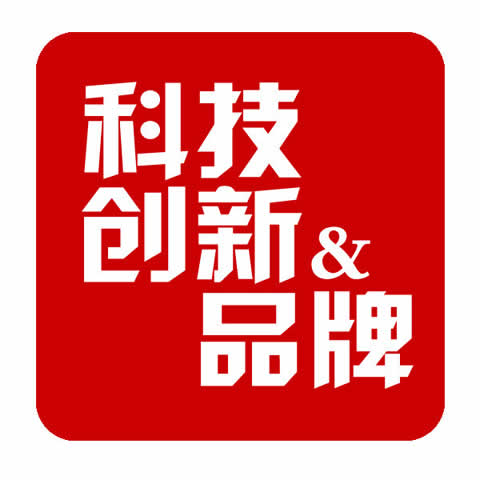